Reflects your good taste
products allows to enjoy the details.

Pipe cutting
01Before production begins, it is necessary to cut the pipe into the relevant segments according to the drawings of future products. Stainless steel pipes require very precise cutting equipment to reduce inaccuracies in connections, waste and use raw materials with maximum efficiency.
Grinding
02Grinding allows to smooth the surface of the pipe, remove roughness and prepare it for welding. Grinding is done automatically on a European equipped machine using abrasives. This step of grinding also allows us to identify the smallest defects before welding and to eliminate the possibility of loss of the highest quality product. After satisfactory grinding control, the pipe is ready for further processing.
Welding
03We use handmade and robotic welding. All welding work takes place in an argon atmosphere (argon-arc welding), which requires high-quality welders, special welding workstations and robotic high-quality equipment. Each welding seam is checked separately visually and technically.
Pressure check
04Each product undergoes a pressure test of 22 bars by air to ensure the high quality of the work of welding masters and absence of leakage. This pressure check is not the first or last, but undoubtedly is the most important of all next check steps.
Welds cleaning
05Handling of weld seams after welding gives elegant and neat appearance of products. Definitely a lot attention is paid to this stage of production. We care about the quality of our products, so we clean all welds seams manually, providing an excellent coupling of ribs.
Electropolishing
06We polish products in special baths by electrolysis to a mirror finish. This emphasizes the nobleness as well strength of stainless steel and removes any scratches received during the manufacturing of the product.
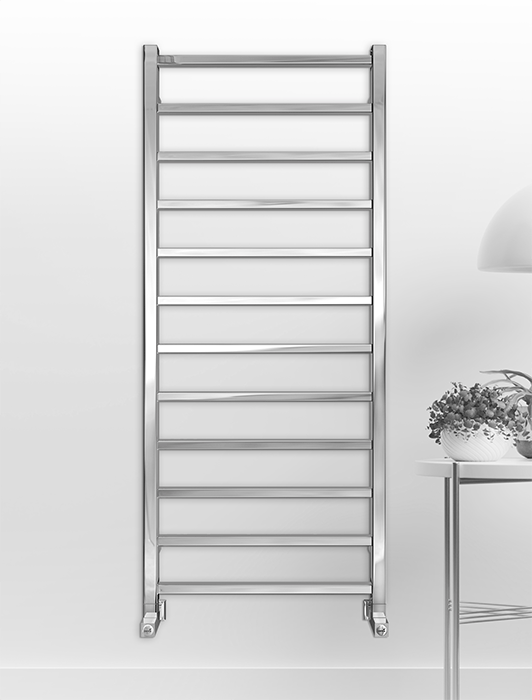